In addition to the products we offer, we also operate as a 3D printing service and can print models that you have designed or obtained elsewhere, with proper licensing. Please contact us for a quote and more information!
How to request a quote
3D printing requires a digital 3D model; the digital file is the “tooling” for this additive manufacturing process. To generate a 3D printing quote, we require a 3D model; it is not possible to estimate printing cost based only on size or photos, as pricing is highly geometry and post-processing dependent. The quickest method is to send us your model file via email at the address at the bottom of the page. If your model is very large or requires additional security, contact us to set up a secure file drop location. If you do not have a 3D model, you can still contact us to see if we can help create your 3D model with the design services we offer.
It is also helpful if you can provide what material, color, quality settings (e.g. nozzle size, layer height, infill, etc.) that you would like, as this will impact the quoting process. If you are unsure, please tell us as much as you can about your application, and we can suggest a suitable process and materials.
Plastic Fused Filament Fabrication (FFF)
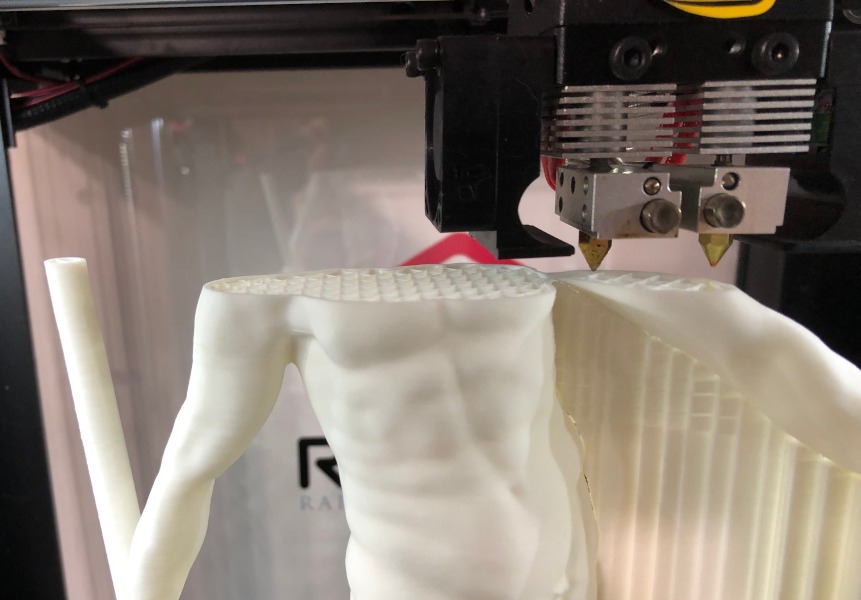
Fused Filament Fabrication (FFF), a.k.a. Fused Deposition Modeling (FDM), is a material extrusion additive manufacturing (AM) process whereby thermoplastic is melted and extruded through a nozzle. The molten plastic is laid down layer-by-layer to form the 3D part. FFF is one of the most common 3D printing processes due to its low cost and ability to utilize a wide range of useful materials.
FFF Materials
We print in a wide variety of thermoplastic materials, and a also willing to use a custom filament for your project, assuming it is supported by our printers. Material sample list:
- PLA (Polylactic Acid)
- PVB (Polyvinyl Butyral)
- ABS (Acrylonitrile Butadiene Styrene)
- ASA (Acrylonitrile Styrene Acrylate)
- Nylon (Polyamide)
- Carbon Fiber filled Nylon
- PETG (Polyethylene Terephthalate Glycol)
- PC (Polycarbonate)
- PP (Polypropylene)
- Filled (Woodfill, Bronzefill, etc.)
- TPU (Thermoplastic Polyurethane)/Flexible
Full Color Gypsum Binder Jetting
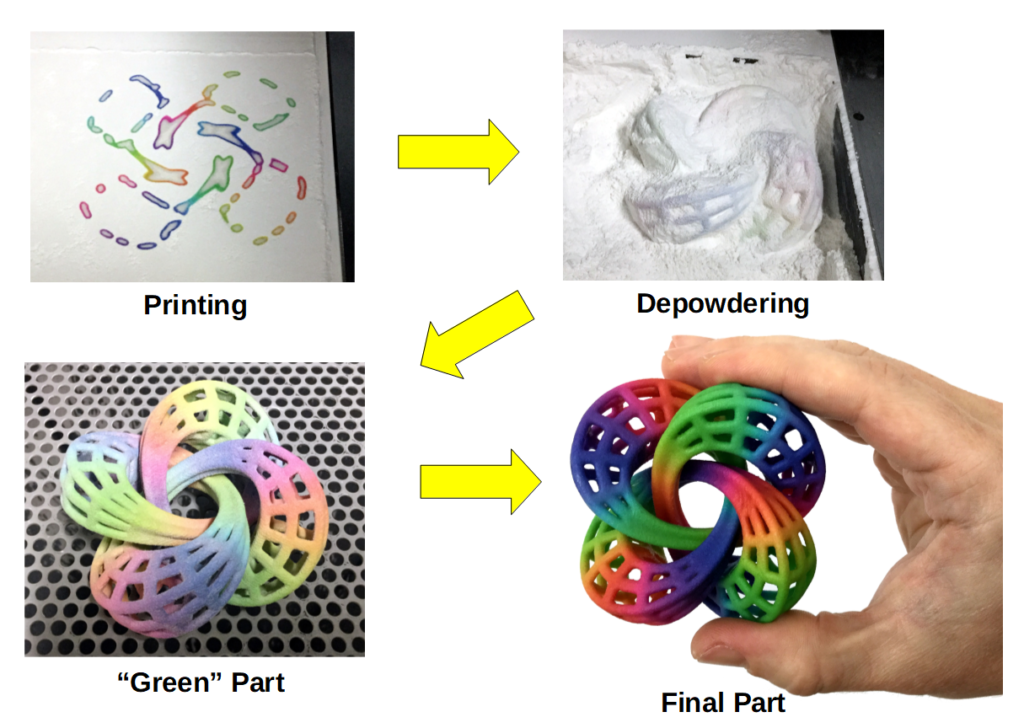
Our Composite Stone products are made using the 3D printing process known as Binder Jetting, using machines manufactured by Z Corp. The process starts with a digital 3D model, which is sliced into thin cross sections (aka layers) and sent to the printer. The printer uses a bed of powder, in this case a gypsum-based powder similar to plaster but specially formulated for 3D printing. An inkjet head moves over the powder bed and selectively deposits a water-based binder, joining the powder in the same shape as the 3D model cross section. At the same time colored ink is applied on the cross section outer edges, creating the colors at the same time as the part. The powder bed then moves down a distance equal to the layer thickness, and a roller deposits another layer of powder on top. The next higher cross section is printed, and this process repeats until all the layers have been printed.
The part is then dried, removed from the bed, and the excess powder is vacuumed or blown off with compressed air, and recycled for the next print. The model is now in the “green” state, and is very porous and fragile. The green models are then infiltrated with a 2-part epoxy resin, which soaks into the powder and fills the pores of the model, adding substantial strength, and saturating the colors. The infiltrated part is then allowed to cure, which may take up to 72 hours.
Full Color
Our process is one of the very few 3D printing processes that can print in full color, using a CMY inkjet printhead to reproduce thousands of individual colors. Many epoxies have a yellow tint, and will yellow further over time with UV exposure, however the resin we use is extremely clear, and is the best non-yellowing formulation on the market today, ensuring that your print will still look great for years to come.
While we do not recommend that you expose the models to water, our internal tests have shown that the models are extremely water resistant, as demonstrated in the following video:
To keep the colors looking great you should limit the exposure of the model to UV light, e.g. keep them indoors and do not place in a window, car, etc. The inks used for the colors may fade with UV exposure, similar to other inkjet prints. The epoxy used is the most UV resistant product on the market today, however long term effects are still unknown at this point, so it’s best to be safe than sorry.
Solid Color or Marbling
Models can also be printed in monochrome (solid white with no colored inks). Pigments are then mixed with the epoxy during the infiltration stage, producing a model that is dyed throughout the infiltration depth, instead of the surface colors in the full color process. These pigments are also much more UV stable than the inks used in the full color process. Many standard colors are available (white, black, grey, blue, green, red, yellow), and the pigments can also be mixed to produce custom colors. Note that this is currently done by hand, and so exact color matching is not guaranteed. Other effects are also possible, such as painting different pigments to achieved a marbled effect.
Solid colors are commonly used for our Fine Art line of products however they can be utilized for any models you choose.
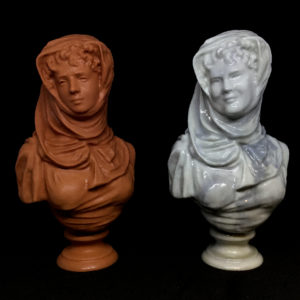
3DLirious continues to innovate and push the boundaries of what is possible, and has developed a line of unique finishes that are offered by no one else. Fine metal, wood, or stone powders are mixed with the epoxy resin, and penetrate into the surface, building up a top layer. Pigments may also be utilized for various effects. Metal infused parts can then be hand polished to produce a shiny metal part, and/or a chemical patina can be applied to produce interesting and artistic effects. Each part produced is unique, and an endless variety of different effects are possible. These finishes can be quite labor intensive to produce (and are priced accordingly), yet still less expensive than 3D printing entirely out of the metal on a metal 3D printer, however we hope you will agree that the final product is worth the effort!
Metals
Various different metals and alloys alloys can be utilized, forming a metal-stone amalgam. These can then be polished or patinas applied for beautiful aging effects.
Copper, Bronze, and Tin with Black Patina
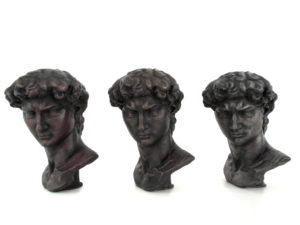
Bronze
A mixture of copper and tin, bronze has been used since antiquity for fine sculptures and art. It can be polished and left as-is (note that crevises and small details cannot be effectively polished), or a patina applied.
Copper
Pure copper powder without pigment. It reacts to patinas similarly to bronze, but with the characteristic reddish copper hue in the polished areas.
Iron
Iron powder produces parts that are black when infiltrated, but can be polished to a shiny dark grey. This can also be reacted with patinas to produce rusty and aged parts. Interestingly, the parts will also be slightly magnetic!
Wood
Fine pecan shell flour creates wood-stone composite parts that are quite convincing and beautiful!
Stone
Fine stone powders of marble, limestone or porcelain create a stone-stone amalgam material. The stone powder also helps to fill the surface porosity and smooth layer lines.
Additional Materials
In addition to the Composite Stone material and finishes above, we also have experience with many other 3D printing technologies and materials. These include a variety of plastics, including high detail resins suitable for small figures, as well as solid metal parts. Please contact us to discuss further to see if we can meet your needs. Note that these materials are produced off-site, and so the lead time is typically longer than our in house material.