Material
The primary material utilized by 3DLirious is Composite Stone. This is composed of powdered stone in an epoxy resin matrix, similar to other engineered composite stone products such as cultured marble or cultured granite, but using gypsum stone instead of marble or granite powder. The final parts are similar in look and feel to ceramic figurines, but are much more durable.
You may see similar materials described as “full color sandstone”, however this is a misnomer, as the parts are composed of gypsum and contain no silica sand. This can be confusing, as there are also 3D printers that print in actual sand, such as those from ExOne and VoxelJet, however these are typically used for industrial sand casting molds, and do not print in full color. In addition, the majority of our competitors infiltrate their prints with cyanoacrylate (aka SuperGlue), which cures very fast, but produces parts that are brittle and not water resistant. Our epoxy infused products take longer to produce, but are much stronger, more durable, and quite water resistant (see below).
Our Composite Stone products are all created on site in our studio in Arlington, call to see when you can stop by to see a demonstration of how it works!
3D Printing Process
Our Composite Stone products are made using the 3D printing process known as Binder Jetting, using machines manufctured by ZCorp. The process starts with a digital 3D model, which is sliced into thin cross sections (aka layers) and sent to the printer. The printer uses a bed of powder, in this case a gypsum-based powder similar to plaster but specially formulated for 3D printing. An inkjet head moves over the powder bed and selectively deposits a water-based binder, joining the powder in the same shape as the 3D model cross section. At the same time colored ink is applied on the cross section outer edges, creating the colors at the same time as the part. The powder bed then moves down a distance equal to the layer thickness, and a roller deposits another layer of powder on top. The next higher cross section is printed, and this process repeats until all the layers have been printed.
The part is then dried, removed from the bed, and the excess powder is vacuumed or blown off with compressed air, and recycled for the next print. The model is now in the “green” state, and is very porous and fragile. The green models are then infiltrated with a 2-part epoxy resin, which soaks into the powder and fills the pores of the model, adding substantial strength, and saturating the colors. The infiltrated part is then allowed to cure, which may take up to 72 hours.
The printers are capable of thousands of different color combinations. Due to color mixing, certain colors are difficult to reproduce consistently, most notably blacks, browns and skin tones, and some variation in the print’s coloring (including from one print to the next) is unavoidable.
Printers: ZCorp Zprinter 450/350
Composite Stone Care and Feeding:
- Prints are fragile and are not toys. They are for decorative purposes only and should be handled carefully, similar to porcelain figurines.
- Do not expose the prints to strong UV light, including direct sunlight. This may cause the colors to fade over the years.
Stainless Steel
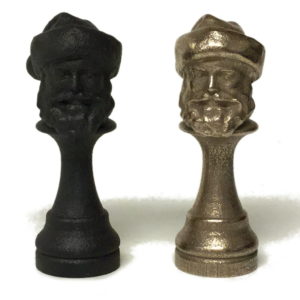
Bronze-infused stainless steel parts are made in a two step process. The first step uses the Binder Jetting 3D printing process with layers of stainless steel powder and a binder. This “green” part is then infused with bronze, which replaces the binder and forms a strong, solid metal part. The color of the final piece can vary from bronze to silver, depending on how the bronze infuses the part. The piece can also be plated with a layer of gold, bronze, or matte black.
Printer: ExOne M-Flex or similar.
Overview of the printing process: